As customer demand increases for innovative, sustainable O-Ring solutions, Datwyler is expanding its production capabilities with new molding machines installed at its sites in China and Mexico. Capable of producing thousands of O-Rings every hour, the new machines will use the latest injection molding technology to produce top quality elastomer components for applications such as battery thermal management, power electronics, transmission, sensors, plus electric braking and driveline systems. Further potential solutions for customers from different industries are also being evaluated.
The new machines in Silao, Mexico and Ningguo, China will join Schattdorf (Switzerland), Daegu (Korea), Ontario (USA), Vandalia (USA) and Viadanica (Italy), widening Datwyler’s manufacturing and development network around the world.
This global network will enhance the Datwyler support to its customers in China and North America looking for local suppliers for increased supply chain security and sustainability.
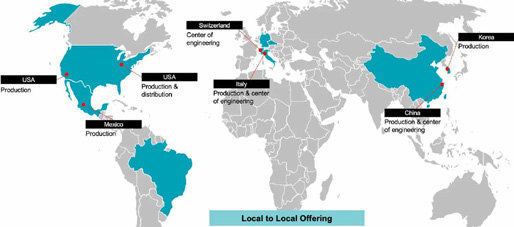
“This local-to-local approach is becoming more and more important to our customers.
It is not only more reliable for our customers to have production plants close to them, but more sustainable in terms of transport. These new machines also provide high levels of automation and unavoidable, process-related waste volumes are as minimal as the current state of the art allows. This also increases the efficiency of the process and makes it as costeffective as possible.”
Richard Katona
Key Account Manager, Business Unit Mobility
“Customers in a broad range of industries are asking for fast, sustainable and innovative O-Ring solutions. With these new machines, we are excited to offer further O-Ring solutions to meet their needs.”
Bernd Meyer
Head of Sales, Business Unit General Industry
The new injection molding machines feature state-of-the-art cold runner technology designed by Datwyler, which offers increased control of the compound temperature, keeping it at a low viscosity for the production of high-precision components. The machines are also highly versatile, able to provide more cavities and therefore more parts per run.
“The new machine allows the compound to be injected into different areas of the tool, as opposed to a single central area. Different injection points mean greater precision and control over the finished product, which ultimately drives waste out of the process. This feeds into our commitment to delivering operational excellence wherever our customers are located, and ensures that parts produced across our manufacturing facilities will be identical and of the same high quality.”
Richard Katona
Key Account Manager, Business Unit Mobility

Alongside increasing its production capabilities, Datwyler is also developing new coating solutions for O-Rings, examining how they can increase not only the efficiency of the production process, but the application itself. Datwyler understands that the market for O-Rings has a huge amount of potential, from mobility and the energy sector to sanitary and air-conditioning technology. Driven by new solutions to satisfy customer needs in the various industries, new applications for O-rings will also emerge. Datwyler is always looking at ways to further expand its knowledge and production capabilities all over the world.
|
|
Datwyler develops surface and coating solutions such as semi-permanent and permanent, PTFE coating, molykote, plasma treatment, polysiloxane, and others for O-rings in its own technology and innovation laboratory.
Katarina Mijatovic
Marketing Manager, Business Unit Mobility